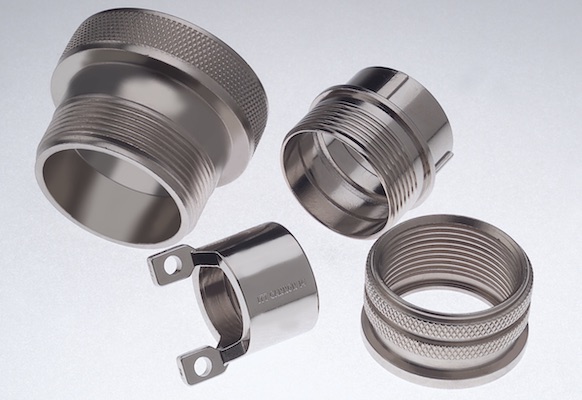
無電解ニッケルメッキとは
無電解ニッケルメッキとは、電気を使用せずにメッキ処理することです。
メッキの膜厚が均一につくため、複雑な製品形状や、寸法精度を有するものに適しており、高精度なニッケルリン皮膜が得られます。
無電解ニッケルメッキ加工は、ステンレス・SUS、鉄鋼素材、銅・銅合金・真鍮、アルミ素材に対応可能です。
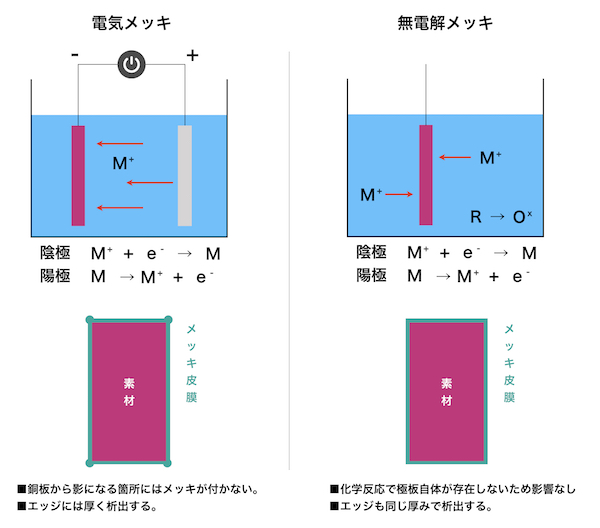
高い寸法精度・形状精度: 均一なメッキの厚み
化学反応でメッキを析出していきますので、メッキ浴の循環によって常に新しいメッキ液が触れるところには、形状、サイズに関わらず均一なメッキ厚が析出します。(μmオーダーの制御が可能です。)
電気メッキでは電極との位置関係により、電気的に陰になる部分にはメッキが全く析出しません。また電気はエッジや鋭利な場所に対して多く流れる性質がありますので、無電解メッキと同レベルの均一なメッキ厚を得ることは難しくなります。
寸法精度が高い製品に対して、電気メッキはメッキをした後に研磨等をし、寸法を調整することが多くなります。無電解メッキではメッキ前に寸法を合わせておくことで、ほとんどの場合でメッキ後の調整は不要となります。
優れた耐食性
無電解ニッケルメッキは、りん濃度が高まると非晶質になります。そのため、結晶質の電気ニッケルメッキに比べて、耐食性に優れた皮膜が得られます。
元々被覆性の高い20μm以上の厚付を行うと、皮膜上にあるピンホールなどの欠陥がなくなり、更に良い耐食性が期待できます。塩素、フッ素などのハロゲン系のガスに対して高い耐食性を備えています。
また、ステンレス材で製作すると非常に高価になってしまうものには、鉄材で製作してからメッキを施すこともできます。そうすることで、安価で目的の耐食性を得るということができ、多くの場面で選ばれています。
熱処理で硬度向上
メッキ後の硬度は最も一般的な中リンタイプの無電解ニッケルメッキの場合で、およそ500HV程度です。さらに熱処理をすることにより結晶質となり、硬度はさらに上がります。
300℃の熱処理をかけることで750HV以上となり、400℃の熱処理では最も硬くなります。耐摩耗性目的で熱処理をして使われることが多く、用途に応じて複合メッキとして使われます。
複合メッキで特性が広がる
フッ素樹脂、セラミック粒子、窒化ホウ素などを添加することによって、色々な特性を得ることができます。
フッ素樹脂を添加することによって摩擦係数を下げ、摺動性を向上させます。回転体あるいは往復摺動部分の静粛性目的で使われることも多くなっています。さらに含有量を多くすることによって、撥水性を持たせることができます。金型の型離れ性も向上するため、離型剤使用量の削減目的にも利用されることがあります。
セラミック粒子は非常に硬く、それを分散させたメッキは耐摩耗性に優れています。環境問題など硬質クロムメッキの代替として使われることも多くなっています。
軽量化
自動車をはじめとして、様々な製品の軽量化の取り組みが盛んです。
さらに、素材を鉄材からアルミ材に変更されることも非常に多くなっています。ただしアルミ材そのものの強度は低いため、メッキをすることで鉄材と同様の強度を持たせることができ、耐久性も高くなります。
絶縁体でもメッキ可能
電気ニッケルメッキは被めっき物が導電性のあるもののみ対応となるため、絶縁体である樹脂などは不可です。無電解ニッケルメッキは電気を使わず、化学反応のみでメッキを析出させていくため、絶縁体でもメッキ可能です。
無電解ニッケルメッキの短所
・電気ニッケルメッキに比べ、浴組成の変動が大きいため管理が難しくなります。
・浴温度が約90℃と高温であるため、熱の影響を受ける製品については注意が必要です。
・電気ニッケルメッキに比べて材料費が高く、メッキ析出速度が電気ニッケルメッキに比べて遅くなります。そのため、加工コストが高くなります。
・浴中に反応生成物質として亜リン酸が蓄積し老化液となるため、メッキ速度が低下し、最終的には廃液となります。